Acerca de

08 ENGINEERING
Assa Abloy - Maintenance Fitter (Manufacturing)
July 2024 - September 2024 (Contract)
Maintenance fitter – Manufacturing.
Duties
-
Diagnosing and Troubleshooting:
-
Identify and resolve faults in equipment reported by the system or operators, such as in brass machining.
-
Disassemble damaged CNC spindles due to crashes caused by data glitches or operator errors, including sourcing and ordering necessary parts.
-
-
Assisting Senior Fitters:
-
Aid senior fitters by dismantling guards and protective equipment to access and repair faulty components like solenoids, airlines, and pneumatic hoses.
-
-
Equipment Maintenance:
-
Tag and safely remove hydraulic hoses and other items needing replacement, particularly when leaks affect performance.
-
Replace and adjust v-belts on linishing machines for a polished finish on door brackets and security-related items.
-
Replace pneumatic valves in production equipment, adjusting airflow to optimize machine speed for operators.
-
-
Machine Refurbishment and Commissioning:
-
Refurbish and re-commission old equipment, such as repairing an old press and creating acrylic guards for operator protection and visibility.
-
-
General Machining and Fabrication:
-
Perform general machining tasks for stainless steel door brackets, including setting up jigs and milling machines.
-
Conduct small-scale manufacturing tasks using MIG welding for brackets and minor equipment repairs (limited by onsite welder availability).
-
-
Preventative Maintenance:
-
Carry out preventative maintenance tasks whenever possible to ensure optimal equipment performance.
-
-
Technical Skills and Tools:
-
Utilize hand tools and specialized equipment specific to Assa Abloy.
-
Apply lubricants, greases, and Molykote grease to address rough-running machines.
-
Read and interpret engineering drawings for complex machinery repairs.
-

Hydraulic lines and hoses replaced due to seizure which caused loss of power and fluid loss on a Nakamura CNC.
Alstom - Mechanical Fitter (Rail Industry)
January 2024 to July 2024 (Contract)
I was employed for a 6 month contract, and these were my duties:
-
Unboxing master, slave, and trailer axles for VLine train bogies with lifting cranes/equipment
-
Unboxing brake discs for VLine train bogies using lifting cranes/equipment
-
Prepping master, slave or trailer axle journals on rotating prepping jig using cranes, and using various grit sandpaper for a desired surface finish for both brake discs and bogie wheels
-
File creation for each axled prepped for record of sizes, surface finish and other details to be kept as a record for each axle being assembled for each train bogie
-
Measuring of diameters of brake disc journals, wheel journals with large size micrometers (Ø212.500 to Ø212.529 for brake discs) to enter in the file to be kept in the records and to find a closely matched disc brake and wheel, e.g. 0.010 is critical for interference fitting
-
Using pallet trucks to transport axles loaded on stillages into the heat room to be kept at a 20°C all year round
-
Using heavy lifting equipment such as slings, lifting jigs, fixtures, etc. to move heavy items around the workshop and into the press
-
Prepping brake discs, wheels for Vline trains, Queensland rail network and other customers so they can be pressed using heavy duty presses to high tolerances and tonnage
-
Using heavy duty presses and other attachments in-order-to press wheels and brake discs for different axles from different projects, master, slave and trailer for train bogies
-
Whenever we strip, we use oil pumps to stretch the wheel or disc brake hubs to be pressed off without any damage or interference
-
Using hand tools such as drills to fasten press tooling on the heavy-duty press, angle grinders to smooth surfaces if there is damage to wheel/brake disc journals if there is pickup
-
Entering data into press in-order-to select the right type of axle, whether we press wheels, or disc brakes or to strip them off the axle
-
Assembling brake discs using torque wrenches to make sure they conform to standards set by the manufacturer and safety
-
Conducting tests on assembled axles also known as ‘runouts’ to document wheel rotation runouts, including brake discs using dial indicators and resistance equipment
-
Using measuring equipment such as long micrometers, verniers, surface finish gauges, rules, etc. to measure and record sizes into the database
-
Taking photographs as evidence for record keeping, for runouts and other legal documents
-
Assembly/stripping of specific items such as axle bearing boxes using lifting equipment
-
Assembly/stripping of axle bearings for master, slave and trailer axles for VLine trains and Queensland Rail Network
-
Application of lubricants, antirust and surface protective substances according to specs
-
Spray painting of wheels and axles whenever doing overhaul or new build mostly for VLine bogies
-
Any other engineering duties as a Mechanical fitter, including small maintenance tasks

Train axle after preparation, pressing of disc brakes and wheels ready for runout measurements.
Tycab - Maintenance Fitter (Cabling Industry)
April 2023 to January 2024
I was employed as a maintenance fitter and die room specialist, here were my dutes:
-
Daily preventative maintenance duties, e.g. Cooling towers and pump room
-
Gearbox fitting and replacement for extrusion machines
-
Pneumatic and hydraulic lines repair and diagnostics
-
Unclogging blocked piping filled with copper and other materials
-
Cleaning capstans for tinning lines for wire to be free of defects and frays
-
Small repairs to wire uptake and dancers, e.g. Bearings, etc.
-
Manufacturing of small components to hold other items to be fixed
-
Fitting and machining using lathes, milling machines and drop saws
-
Hand tools such as drills, angle grinders both battery and electric
-
Proficient using pedestal drills and grinders, also linishers
-
Welding of metal panels at the production lines
-
Other manufacturing of support beams, machine safety items, etc.
-
Use of spray paints to colour manufactured frames and other items
-
Cleaning of dies for manufacturing of extrusion lines of different diameters
-
Use of ovens and solvents to help remove rubber and other materials for production
-
Correct application of lubricants for gearboxes, cooling lines, and other assemblies
-
Assembling pulley assemblies for coiling machines (upcast machines)
-
Removing of bearing shafts of various sizes and diameters
-
Some forklift work (I have to be retested) for my license
-
Able to use scissor lifts and ladders safely
-
Filling gas bottles for flame torches and other uses
-
Able to read drawings and other engineering diagrams
-
OH&S trained and able to train small groups
-
Former engineering instructor at HMAS Cerberus teaching entry level mechanical engineering
-
Other small welding duties, and developing such skills
-
Able to assembly components to specifications to designated tolerances
-
Basic metal fabrication using MIG and Oxy cutting
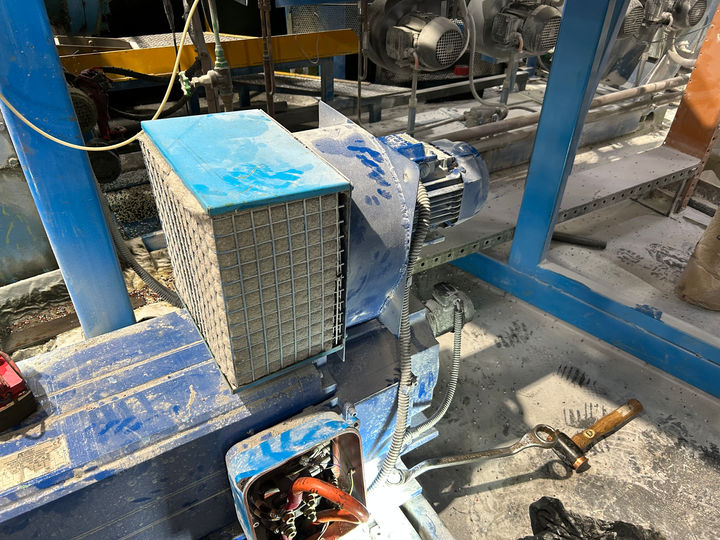
We replaced an electric motor and there was a lot of talc powder to help the PVC flow and melt with the cable.
SMA Inc. - Mechanical Technical Instructor (Marine Engineering) - HMAS Cerberus
November 2004 to November 2010
I was employed as a technical instructor (stoker) and training developer, my dutes were:
-
Instructing Navy and Air Force student in OH&S, 3 points of contact, safe lift individually and in teams while keeping lower back straight
-
Basic marking-out and lay-out using dies and how to safely handle it, using scribers, protractors, squares, magnetic blocks, surface tables
-
How to shape metal objects using hammers, chisels, and scrapers
-
Delivering training in basic hand tools such as hacksaws and selecting the right size blade and number of teeth for different materials
-
Cutting and shaping of aluminium panels, marking out component locations for electronic assemblies for both Electric and Electronic streams
-
Introduction to measuring equipment such as micrometers, verniers, height gauges, internal gauges, depth gauges/micrometers, rules, compasses, tape measures
-
Teaching students how to safely use electric angle grinders and drills
-
Instructing students how to use pneumatic drills and angle grinders
-
Safe use of pedestal drills and how to change speeds safely
-
How to use clamps, vices and clamping kits to drill odd shape components
-
Delivery of theory lessons in a classroom environment
-
Exam delivery and observation (2nd Instructor) and remedial/tutorial lessons
-
Delivering Engineering Drawing as a subject both theory and practice
-
Reporting of near misses and accidents to the course implementation officer
-
Machine shop OH&S and general upkeep to prevent accidents, etc.
-
Teaching how to safely use lathes and how to set up 3 or 4 jaw chucks
-
Safe use of milling machines, setting up vices, angle plates with slow and fast traverse using various types of cutters
-
How to effectively set up indexing heads and what cutters to use to achieve different shapes and cuts for student projects
-
Using cut-off saws to cut various sizes and lengths materials to help resupply the stores
-
Setting up and safe use of bandsaws and how to replace broken blades
-
Use of surface and offhand grinders to more advanced students to achieve smoother surfaces
CVP Australia - QA Inspector - PBR Brakes, East Bentleigh
February 2004 to November 2004 (Contract)
Here were my duties:
-
Checking brake assemblies for lose parts on the production line before boxing them
-
Assisting production line workers when batches were bigger than they could handle
-
Checking pistons, rotors, breaks and assemblies for porosity and surface defects
-
Checking chrome finish and surface finishing for acceptable tolerances and defects
-
Making sure chemical processes were within the acceptable tolerance
-
Writing reports on pass/fail parts daily using the computer system
-
Organising work for the afternoon shift and reporting any issues.
-
OH&S reporting and monitoring and induction to new team members
-
Metrology, measuring piston heads, ram rods for diameter, height and using surface gauges to check for surface finish and report any defects on a daily log
-
Some stocktaking and warehousing duties and responsibilities.
HdH Components/Boeing - Overhaul Fitter
February 1995 to February 2001
Here were my duties
-
Rubber molding and preparation manufacturing different components such as Nulka Penguin missile sleeves
-
Part marking, identification, and classification of parts to be shifted to clients
-
Production work using honing machines for various components to tolerances of 0.05mm
-
Use of surface grinders to very fine surface finishes for different types of metals such as mild steel, stainless steel, copper, and bronze
-
Use of different CNC machines (limited programming) mostly Mazaks and other milling machines using different clamping methods
-
Use of pneumatic and electric drills and angle grinders to clean and de-burr sharp edges for small and large components
-
Cleanroom duties such as disassembly, surveying and assessing assemblies to be refurbished and repaired according to the Australian Defence Force repair and maintenance manuals
-
Survey, cleaning, disassembly, and refurbishment of various military aircraft components such as C130 Hercules Nose and Main Wheels, F18 Torque Arms, F11 Parts, Caribou Nose and Main Wheels
-
Chemical treatment of various components such as Alodine baths, anodising and degreasing any other components
-
Bead and sand blasting of small to large size components to be chemically treated, primed and painted
-
Stock taking and ordering of various components when conducting refurbishment and surveying of various controlled military parts
-
Survey, disassembly, refurbishment of Vic Metro train powerheads with electrical and hydraulic bi-directional settings (load and response time)
-
Pressure testing of brake assemblies using high pressure rigs
-
Priming and Spray painting of different size components, from small couplings, tie rods to Nose and Main Wheels for C130 Hercules, Caribou, F11, F18 and many more
-
Preparing 2 and 3-part paints and conducting viscosity testing before spray painting
-
Use and application of sealing materials, curing using ovens at set temperatures in different size ovens
-
Removing bearing cups heating wheel assemblies, with presses and replacing new bearing cups with liquid nitrogen and to apply other sealants and anti-corrosion pastes and gels
